In conditions like this, the traditional methods of condition monitoring would have proved challenging. Thankfully, machine health monitoring has undergone a significant transformation over the years, evolving from rudimentary manual inspections to sophisticated, technology-driven systems. Traditionally, maintenance teams relied on periodic checks and scheduled maintenance routines, often using basic tools. This approach, while effective to a degree, was inherently reactive, addressing issues only after they had manifested, which frequently led to unexpected downtimes and costly repairs. The limitations of manual monitoring became increasingly apparent as industrial machinery grew more complex and the demand for operational efficiency intensified.
The advent of digital technology marked a pivotal shift in machine health monitoring. The introduction of wired sensors allowed for continuous data collection, providing more timely insights into machine conditions. However, these are often cumbersome, expensive to install, and difficult to maintain, particularly in harsh or remote environments. The real game-changer has been the development of wireless sensors and remote data monitoring solutions. These innovations enable real-time, continuous monitoring without the need for extensive wiring, making it easier and more cost-effective to deploy. Advanced analytics and machine learning algorithms further enhance the capability to predict and prevent failures, moving from reactive to proactive and predictive maintenance strategies. Today, cutting-edge wireless sensors, such as those offered by Erbessd-Instruments, a global powerhouse in Machine Health, provide unparalleled accuracy, reliability, and ease of use, setting new standards for machine health monitoring across various industries.
Using the Cloud
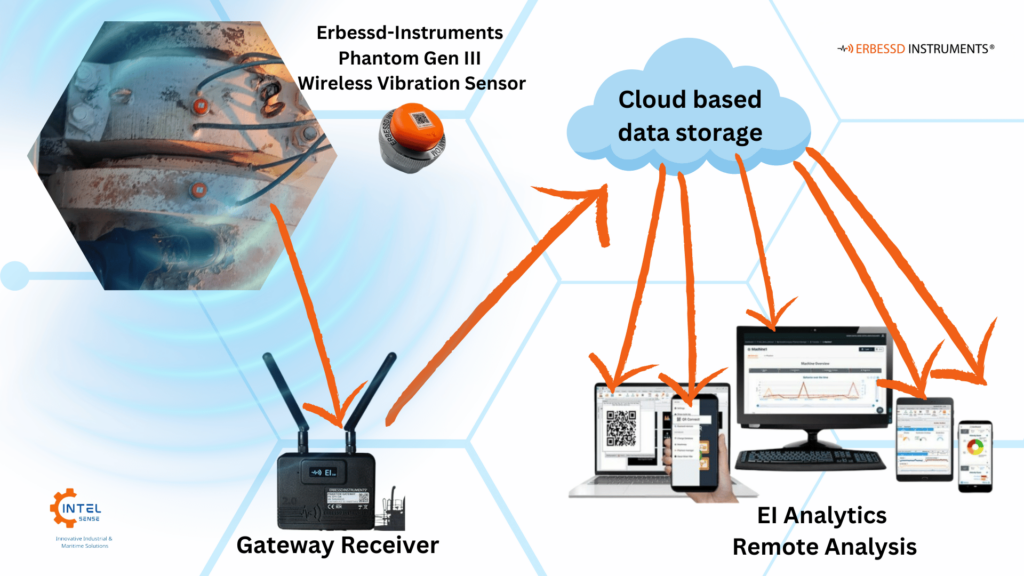
Cloud-based data collection offers numerous advantages that enhance the overall effectiveness and efficiency of maintenance strategies. By leveraging cloud technology, data from wireless sensors can be collected, stored, and analyzed in real-time, irrespective of geographic location. This ensures that critical information is accessible to maintenance teams and decision-makers at any time and from anywhere, facilitating timely interventions and informed decision-making.
The scalability of cloud-based solutions allows for seamless integration of new sensors and expansion of monitoring systems as operations grow. Moreover, advanced data analytics and machine learning algorithms can be applied to vast datasets stored in the cloud, enabling more accurate predictive maintenance and early detection of potential issues. This proactive approach minimizes downtime, reduces maintenance costs, and extends the lifespan of machinery.
Additionally, cloud-based systems offer enhanced data security and redundancy, ensuring that valuable information is protected and recoverable in the event of local hardware failures. In essence, cloud-based data collection empowers businesses to harness the full potential of their machine health monitoring systems, leading to more reliable, efficient, and cost-effective operations.
Wired or Wireless?Â
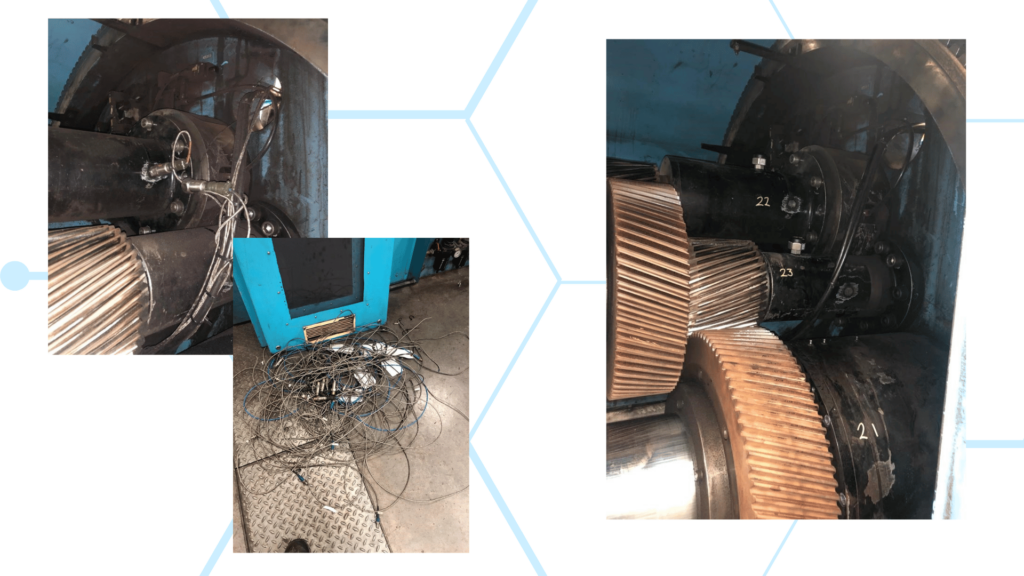
Wireless condition monitoring systems offer significant advantages over wired systems, particularly in challenging and hazardous environments like power plants and cement manufacturing facilities.
Wired: The installation of wired systems in such settings is often fraught with difficulties, including the need for extensive cabling, which can be both costly and time-consuming. Additionally, wired connections are susceptible to damage from harsh environmental conditions, such as high temperatures, dust, and vibrations, which are common in these industries. Wired systems may come with guarantees for cable replacements, but the lost downtime in awaiting repairs is still a cost.
Wireless: In contrast, Erbessd-Instruments’ wireless condition monitoring systems eliminate the need for complex cabling, making installation quicker, easier, and more cost-effective. Wireless sensors are designed to withstand extreme conditions, ensuring reliable performance and continuous data transmission even in the most demanding environments. This durability and ease of deployment not only enhances safety by reducing the need for maintenance personnel to enter hazardous areas but also ensures that critical machinery health data is consistently collected and monitored.
Consequently, wireless condition monitoring systems enable more effective predictive maintenance, minimizing downtime and operational disruptions while maximizing the lifespan and efficiency of machinery in power plants and cement manufacturing operations.